ਚੁੰਬਕੀ ਸਮੱਗਰੀ ਨੂੰ ਦੋ ਸ਼੍ਰੇਣੀਆਂ ਵਿੱਚ ਵੰਡਿਆ ਜਾ ਸਕਦਾ ਹੈ: ਆਈਸੋਟ੍ਰੋਪਿਕ ਮੈਗਨੇਟ ਅਤੇ ਐਨੀਸੋਟ੍ਰੋਪਿਕ ਮੈਗਨੇਟ:
ਆਈਸੋਟ੍ਰੋਪਿਕ ਚੁੰਬਕ ਸਾਰੀਆਂ ਦਿਸ਼ਾਵਾਂ ਵਿੱਚ ਇੱਕੋ ਜਿਹੇ ਚੁੰਬਕੀ ਗੁਣਾਂ ਨੂੰ ਪ੍ਰਦਰਸ਼ਿਤ ਕਰਦੇ ਹਨ ਅਤੇ ਕਿਸੇ ਵੀ ਦਿਸ਼ਾ ਵਿੱਚ ਚੁੰਬਕੀਕਰਨ ਕੀਤਾ ਜਾ ਸਕਦਾ ਹੈ।
ਐਨੀਸੋਟ੍ਰੋਪਿਕ ਚੁੰਬਕ ਵੱਖ-ਵੱਖ ਦਿਸ਼ਾਵਾਂ ਵਿੱਚ ਵੱਖ-ਵੱਖ ਚੁੰਬਕੀ ਗੁਣਾਂ ਨੂੰ ਪ੍ਰਦਰਸ਼ਿਤ ਕਰਦੇ ਹਨ, ਅਤੇ ਉਹਨਾਂ ਕੋਲ ਅਨੁਕੂਲ ਚੁੰਬਕੀ ਕਾਰਗੁਜ਼ਾਰੀ ਲਈ ਇੱਕ ਤਰਜੀਹੀ ਦਿਸ਼ਾ ਹੁੰਦੀ ਹੈ, ਜਿਸਨੂੰ ਸਥਿਤੀ ਦਿਸ਼ਾ ਵਜੋਂ ਜਾਣਿਆ ਜਾਂਦਾ ਹੈ।
ਆਮ ਐਨੀਸੋਟ੍ਰੋਪਿਕ ਮੈਗਨੇਟ ਸ਼ਾਮਲ ਹਨਸਿੰਟਰਡ NdFeBਅਤੇsintered SmCo, ਜੋ ਕਿ ਦੋਵੇਂ ਸਖ਼ਤ ਚੁੰਬਕੀ ਸਮੱਗਰੀ ਹਨ।
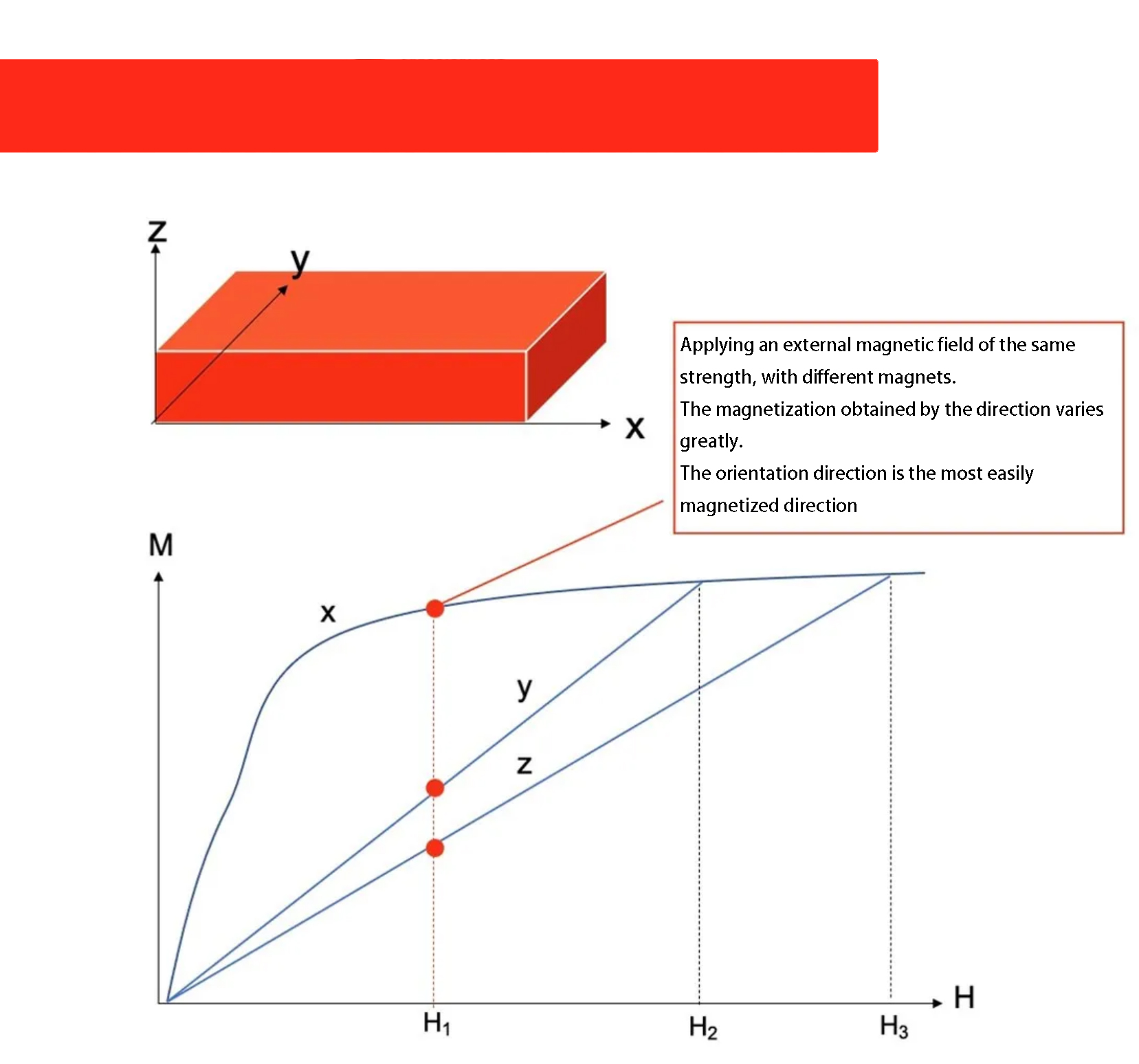
ਸਿੰਟਰਡ NdFeB ਮੈਗਨੇਟ ਦੇ ਉਤਪਾਦਨ ਵਿੱਚ ਓਰੀਐਂਟੇਸ਼ਨ ਇੱਕ ਮਹੱਤਵਪੂਰਨ ਪ੍ਰਕਿਰਿਆ ਹੈ
ਇੱਕ ਚੁੰਬਕ ਦਾ ਚੁੰਬਕਵਾਦ ਚੁੰਬਕੀ ਕ੍ਰਮ ਤੋਂ ਉਤਪੰਨ ਹੁੰਦਾ ਹੈ (ਜਿੱਥੇ ਵਿਅਕਤੀਗਤ ਚੁੰਬਕੀ ਡੋਮੇਨ ਇੱਕ ਖਾਸ ਦਿਸ਼ਾ ਵਿੱਚ ਇਕਸਾਰ ਹੁੰਦੇ ਹਨ)। ਸਿੰਟਰਡ NdFeB ਮੋਲਡਾਂ ਦੇ ਅੰਦਰ ਚੁੰਬਕੀ ਪਾਊਡਰ ਨੂੰ ਸੰਕੁਚਿਤ ਕਰਕੇ ਬਣਾਇਆ ਜਾਂਦਾ ਹੈ। ਇਸ ਪ੍ਰਕਿਰਿਆ ਵਿੱਚ ਚੁੰਬਕੀ ਪਾਊਡਰ ਨੂੰ ਇੱਕ ਉੱਲੀ ਵਿੱਚ ਰੱਖਣਾ, ਇਲੈਕਟ੍ਰੋਮੈਗਨੇਟ ਦੀ ਵਰਤੋਂ ਕਰਕੇ ਇੱਕ ਮਜ਼ਬੂਤ ਚੁੰਬਕੀ ਖੇਤਰ ਨੂੰ ਲਾਗੂ ਕਰਨਾ, ਅਤੇ ਪਾਊਡਰ ਦੇ ਆਸਾਨ ਚੁੰਬਕੀਕਰਣ ਧੁਰੇ ਨੂੰ ਇਕਸਾਰ ਕਰਨ ਲਈ ਇੱਕ ਪ੍ਰੈਸ ਨਾਲ ਦਬਾਅ ਪਾਉਣਾ ਸ਼ਾਮਲ ਹੈ। ਦਬਾਉਣ ਤੋਂ ਬਾਅਦ, ਗ੍ਰੀਨ ਬਾਡੀਜ਼ ਨੂੰ ਡੀਮੈਗਨੇਟਾਈਜ਼ ਕੀਤਾ ਜਾਂਦਾ ਹੈ, ਉੱਲੀ ਤੋਂ ਹਟਾ ਦਿੱਤਾ ਜਾਂਦਾ ਹੈ, ਅਤੇ ਚੰਗੀ ਤਰ੍ਹਾਂ-ਅਧਾਰਿਤ ਚੁੰਬਕੀਕਰਣ ਦਿਸ਼ਾਵਾਂ ਦੇ ਨਾਲ ਨਤੀਜੇ ਵਜੋਂ ਖਾਲੀ ਥਾਂਵਾਂ ਪ੍ਰਾਪਤ ਕੀਤੀਆਂ ਜਾਂਦੀਆਂ ਹਨ। ਇਹਨਾਂ ਖਾਲੀ ਥਾਂਵਾਂ ਨੂੰ ਗਾਹਕ ਦੀਆਂ ਲੋੜਾਂ ਦੇ ਅਨੁਸਾਰ ਅੰਤਿਮ ਚੁੰਬਕੀ ਸਟੀਲ ਉਤਪਾਦ ਬਣਾਉਣ ਲਈ ਨਿਰਧਾਰਤ ਮਾਪਾਂ ਵਿੱਚ ਕੱਟਿਆ ਜਾਂਦਾ ਹੈ।
ਪਾਊਡਰ ਸਥਿਤੀ ਉੱਚ-ਪ੍ਰਦਰਸ਼ਨ ਵਾਲੇ NdFeB ਸਥਾਈ ਚੁੰਬਕ ਪੈਦਾ ਕਰਨ ਵਿੱਚ ਇੱਕ ਮਹੱਤਵਪੂਰਨ ਪ੍ਰਕਿਰਿਆ ਹੈ। ਖਾਲੀ ਉਤਪਾਦਨ ਪੜਾਅ ਦੇ ਦੌਰਾਨ ਸਥਿਤੀ ਦੀ ਗੁਣਵੱਤਾ ਵੱਖ-ਵੱਖ ਕਾਰਕਾਂ ਦੁਆਰਾ ਪ੍ਰਭਾਵਿਤ ਹੁੰਦੀ ਹੈ, ਜਿਸ ਵਿੱਚ ਓਰੀਐਂਟੇਸ਼ਨ ਫੀਲਡ ਦੀ ਤਾਕਤ, ਪਾਊਡਰ ਕਣ ਦੀ ਸ਼ਕਲ ਅਤੇ ਆਕਾਰ, ਬਣਾਉਣ ਦਾ ਤਰੀਕਾ, ਅਨੁਕੂਲਨ ਖੇਤਰ ਦਾ ਅਨੁਸਾਰੀ ਸਥਿਤੀ ਅਤੇ ਦਬਾਅ ਬਣਾਉਣਾ, ਅਤੇ ਓਰੀਐਂਟਡ ਪਾਊਡਰ ਦੀ ਢਿੱਲੀ ਘਣਤਾ ਸ਼ਾਮਲ ਹੈ।
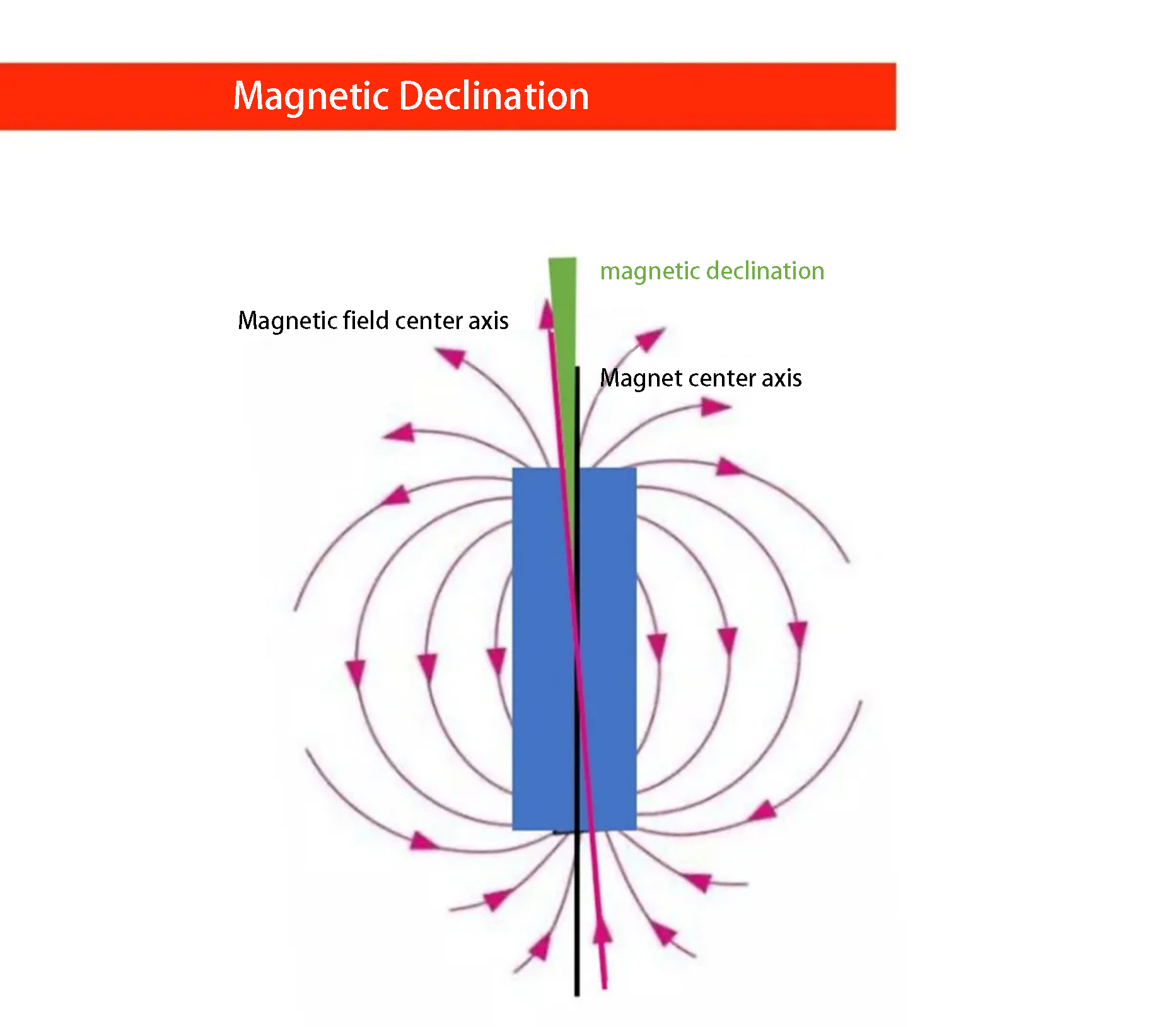
ਪੋਸਟ-ਪ੍ਰੋਸੈਸਿੰਗ ਪੜਾਅ ਵਿੱਚ ਪੈਦਾ ਹੋਏ ਚੁੰਬਕੀ ਸਕਿਊ ਦਾ ਚੁੰਬਕ ਦੇ ਚੁੰਬਕੀ ਖੇਤਰ ਦੀ ਵੰਡ 'ਤੇ ਇੱਕ ਖਾਸ ਪ੍ਰਭਾਵ ਹੁੰਦਾ ਹੈ।
ਚੁੰਬਕੀਕਰਣ ਨੂੰ ਚੁੰਬਕਤਾ ਪ੍ਰਦਾਨ ਕਰਨ ਦਾ ਅੰਤਮ ਕਦਮ ਹੈਸਿੰਟਰਡ NdFeB.
ਚੁੰਬਕੀ ਖਾਲੀਆਂ ਨੂੰ ਲੋੜੀਂਦੇ ਮਾਪਾਂ ਵਿੱਚ ਕੱਟਣ ਤੋਂ ਬਾਅਦ, ਉਹ ਪ੍ਰਕਿਰਿਆਵਾਂ ਵਿੱਚੋਂ ਗੁਜ਼ਰਦੇ ਹਨ ਜਿਵੇਂ ਕਿ ਖੋਰ ਨੂੰ ਰੋਕਣ ਲਈ ਇਲੈਕਟ੍ਰੋਪਲੇਟਿੰਗ ਅਤੇ ਅੰਤਿਮ ਚੁੰਬਕ ਬਣ ਜਾਂਦੇ ਹਨ। ਹਾਲਾਂਕਿ, ਇਸ ਪੜਾਅ 'ਤੇ, ਚੁੰਬਕ ਬਾਹਰੀ ਚੁੰਬਕਤਾ ਨੂੰ ਪ੍ਰਦਰਸ਼ਿਤ ਨਹੀਂ ਕਰਦੇ ਹਨ ਅਤੇ "ਚਾਰਜਿੰਗ ਮੈਗਨੇਟਿਜ਼ਮ" ਵਜੋਂ ਜਾਣੀ ਜਾਂਦੀ ਇੱਕ ਪ੍ਰਕਿਰਿਆ ਦੁਆਰਾ ਚੁੰਬਕੀਕਰਨ ਦੀ ਲੋੜ ਹੁੰਦੀ ਹੈ।
ਚੁੰਬਕੀਕਰਨ ਲਈ ਵਰਤੇ ਜਾਣ ਵਾਲੇ ਸਾਜ਼-ਸਾਮਾਨ ਨੂੰ ਚੁੰਬਕੀ ਜਾਂ ਚੁੰਬਕੀ ਮਸ਼ੀਨ ਕਿਹਾ ਜਾਂਦਾ ਹੈ। ਮੈਗਨੇਟਾਈਜ਼ਰ ਪਹਿਲਾਂ ਉੱਚ ਡੀਸੀ ਵੋਲਟੇਜ (ਭਾਵ, ਊਰਜਾ ਸਟੋਰ ਕਰਦਾ ਹੈ) ਦੇ ਨਾਲ ਇੱਕ ਕੈਪੈਸੀਟਰ ਨੂੰ ਚਾਰਜ ਕਰਦਾ ਹੈ, ਫਿਰ ਇਸਨੂੰ ਬਹੁਤ ਘੱਟ ਪ੍ਰਤੀਰੋਧ ਦੇ ਨਾਲ ਇੱਕ ਕੋਇਲ (ਚੁੰਬਕੀਕਰਨ ਫਿਕਸਚਰ) ਰਾਹੀਂ ਡਿਸਚਾਰਜ ਕਰਦਾ ਹੈ। ਡਿਸਚਾਰਜ ਪਲਸ ਦਾ ਸਿਖਰ ਕਰੰਟ ਬਹੁਤ ਜ਼ਿਆਦਾ ਹੋ ਸਕਦਾ ਹੈ, ਹਜ਼ਾਰਾਂ ਐਂਪੀਅਰ ਤੱਕ ਪਹੁੰਚਦਾ ਹੈ। ਇਹ ਮੌਜੂਦਾ ਨਬਜ਼ ਚੁੰਬਕੀਕਰਨ ਫਿਕਸਚਰ ਦੇ ਅੰਦਰ ਇੱਕ ਸ਼ਕਤੀਸ਼ਾਲੀ ਚੁੰਬਕੀ ਖੇਤਰ ਪੈਦਾ ਕਰਦੀ ਹੈ, ਜੋ ਅੰਦਰ ਰੱਖੇ ਚੁੰਬਕ ਨੂੰ ਸਥਾਈ ਤੌਰ 'ਤੇ ਚੁੰਬਕੀਕਰਨ ਕਰਦੀ ਹੈ।
ਚੁੰਬਕੀਕਰਣ ਪ੍ਰਕਿਰਿਆ ਦੇ ਦੌਰਾਨ ਦੁਰਘਟਨਾਵਾਂ ਹੋ ਸਕਦੀਆਂ ਹਨ, ਜਿਵੇਂ ਕਿ ਅਧੂਰੀ ਸੰਤ੍ਰਿਪਤਾ, ਮੈਗਨੇਟਾਈਜ਼ਰ ਦੇ ਖੰਭਿਆਂ ਦਾ ਫਟਣਾ, ਅਤੇ ਮੈਗਨੇਟ ਦਾ ਟੁੱਟਣਾ।
ਅਧੂਰੀ ਸੰਤ੍ਰਿਪਤਾ ਮੁੱਖ ਤੌਰ 'ਤੇ ਨਾਕਾਫ਼ੀ ਚਾਰਜਿੰਗ ਵੋਲਟੇਜ ਦੇ ਕਾਰਨ ਹੁੰਦੀ ਹੈ, ਜਿੱਥੇ ਕੋਇਲ ਦੁਆਰਾ ਉਤਪੰਨ ਚੁੰਬਕੀ ਖੇਤਰ ਚੁੰਬਕ ਦੇ ਸੰਤ੍ਰਿਪਤ ਚੁੰਬਕੀਕਰਨ ਦੇ 1.5 ਤੋਂ 2 ਗੁਣਾ ਤੱਕ ਨਹੀਂ ਪਹੁੰਚਦਾ ਹੈ।
ਮਲਟੀਪੋਲ ਚੁੰਬਕੀਕਰਨ ਲਈ, ਮੋਟੇ ਦਿਸ਼ਾ ਨਿਰਦੇਸ਼ਾਂ ਵਾਲੇ ਚੁੰਬਕ ਵੀ ਪੂਰੀ ਤਰ੍ਹਾਂ ਸੰਤ੍ਰਿਪਤ ਹੋਣ ਲਈ ਚੁਣੌਤੀਪੂਰਨ ਹੁੰਦੇ ਹਨ। ਇਹ ਇਸ ਲਈ ਹੈ ਕਿਉਂਕਿ ਮੈਗਨੇਟਾਈਜ਼ਰ ਦੇ ਉੱਪਰਲੇ ਅਤੇ ਹੇਠਲੇ ਖੰਭਿਆਂ ਵਿਚਕਾਰ ਦੂਰੀ ਬਹੁਤ ਜ਼ਿਆਦਾ ਹੈ, ਨਤੀਜੇ ਵਜੋਂ ਇੱਕ ਸਹੀ ਬੰਦ ਚੁੰਬਕੀ ਸਰਕਟ ਬਣਾਉਣ ਲਈ ਖੰਭਿਆਂ ਤੋਂ ਨਾਕਾਫ਼ੀ ਚੁੰਬਕੀ ਖੇਤਰ ਦੀ ਤਾਕਤ ਹੁੰਦੀ ਹੈ। ਨਤੀਜੇ ਵਜੋਂ, ਚੁੰਬਕੀਕਰਣ ਪ੍ਰਕਿਰਿਆ ਵਿਗਾੜ ਵਾਲੇ ਚੁੰਬਕੀ ਧਰੁਵਾਂ ਅਤੇ ਨਾਕਾਫ਼ੀ ਫੀਲਡ ਤਾਕਤ ਦਾ ਕਾਰਨ ਬਣ ਸਕਦੀ ਹੈ।
ਮੈਗਨੇਟਾਈਜ਼ਰ ਦੇ ਖੰਭਿਆਂ ਦਾ ਚੀਰਨਾ ਮੁੱਖ ਤੌਰ 'ਤੇ ਵੋਲਟੇਜ ਨੂੰ ਬਹੁਤ ਜ਼ਿਆਦਾ ਸੈੱਟ ਕਰਨ ਕਰਕੇ ਹੁੰਦਾ ਹੈ, ਮੈਗਨੇਟਾਈਜ਼ਿੰਗ ਮਸ਼ੀਨ ਦੀ ਸੁਰੱਖਿਅਤ ਵੋਲਟੇਜ ਸੀਮਾ ਤੋਂ ਵੱਧ ਜਾਂਦਾ ਹੈ।
ਅਸੰਤ੍ਰਿਪਤ ਚੁੰਬਕ ਜਾਂ ਚੁੰਬਕ ਜੋ ਅੰਸ਼ਕ ਤੌਰ 'ਤੇ ਡੀਮੈਗਨੇਟਾਈਜ਼ ਕੀਤੇ ਗਏ ਹਨ ਉਹਨਾਂ ਦੇ ਸ਼ੁਰੂਆਤੀ ਵਿਗਾੜ ਵਾਲੇ ਚੁੰਬਕੀ ਡੋਮੇਨਾਂ ਦੇ ਕਾਰਨ ਸੰਤ੍ਰਿਪਤ ਕਰਨਾ ਵਧੇਰੇ ਮੁਸ਼ਕਲ ਹੁੰਦਾ ਹੈ। ਸੰਤ੍ਰਿਪਤਾ ਪ੍ਰਾਪਤ ਕਰਨ ਲਈ, ਇਹਨਾਂ ਡੋਮੇਨਾਂ ਦੇ ਵਿਸਥਾਪਨ ਅਤੇ ਰੋਟੇਸ਼ਨ ਦੇ ਵਿਰੋਧ ਨੂੰ ਦੂਰ ਕਰਨ ਦੀ ਲੋੜ ਹੈ। ਹਾਲਾਂਕਿ, ਅਜਿਹੇ ਮਾਮਲਿਆਂ ਵਿੱਚ ਜਿੱਥੇ ਇੱਕ ਚੁੰਬਕ ਪੂਰੀ ਤਰ੍ਹਾਂ ਨਾਲ ਸੰਤ੍ਰਿਪਤ ਨਹੀਂ ਹੁੰਦਾ ਹੈ ਜਾਂ ਇਸਦਾ ਬਕਾਇਆ ਚੁੰਬਕੀਕਰਨ ਹੁੰਦਾ ਹੈ, ਇਸਦੇ ਅੰਦਰ ਉਲਟ ਚੁੰਬਕੀ ਖੇਤਰ ਦੇ ਖੇਤਰ ਹੁੰਦੇ ਹਨ। ਭਾਵੇਂ ਅਗਾਂਹ ਜਾਂ ਉਲਟ ਦਿਸ਼ਾ ਵਿੱਚ ਚੁੰਬਕੀਕਰਨ ਹੋਵੇ, ਕੁਝ ਖੇਤਰਾਂ ਵਿੱਚ ਉਲਟ ਚੁੰਬਕੀਕਰਨ ਦੀ ਲੋੜ ਹੁੰਦੀ ਹੈ, ਇਹਨਾਂ ਖੇਤਰਾਂ ਵਿੱਚ ਅੰਦਰੂਨੀ ਜ਼ਬਰਦਸਤੀ ਸ਼ਕਤੀ ਨੂੰ ਕਾਬੂ ਕਰਨ ਦੀ ਲੋੜ ਹੁੰਦੀ ਹੈ। ਇਸ ਲਈ, ਚੁੰਬਕੀਕਰਨ ਲਈ ਸਿਧਾਂਤਕ ਤੌਰ 'ਤੇ ਲੋੜ ਤੋਂ ਵੱਧ ਮਜ਼ਬੂਤ ਚੁੰਬਕੀ ਖੇਤਰ ਜ਼ਰੂਰੀ ਹੈ।
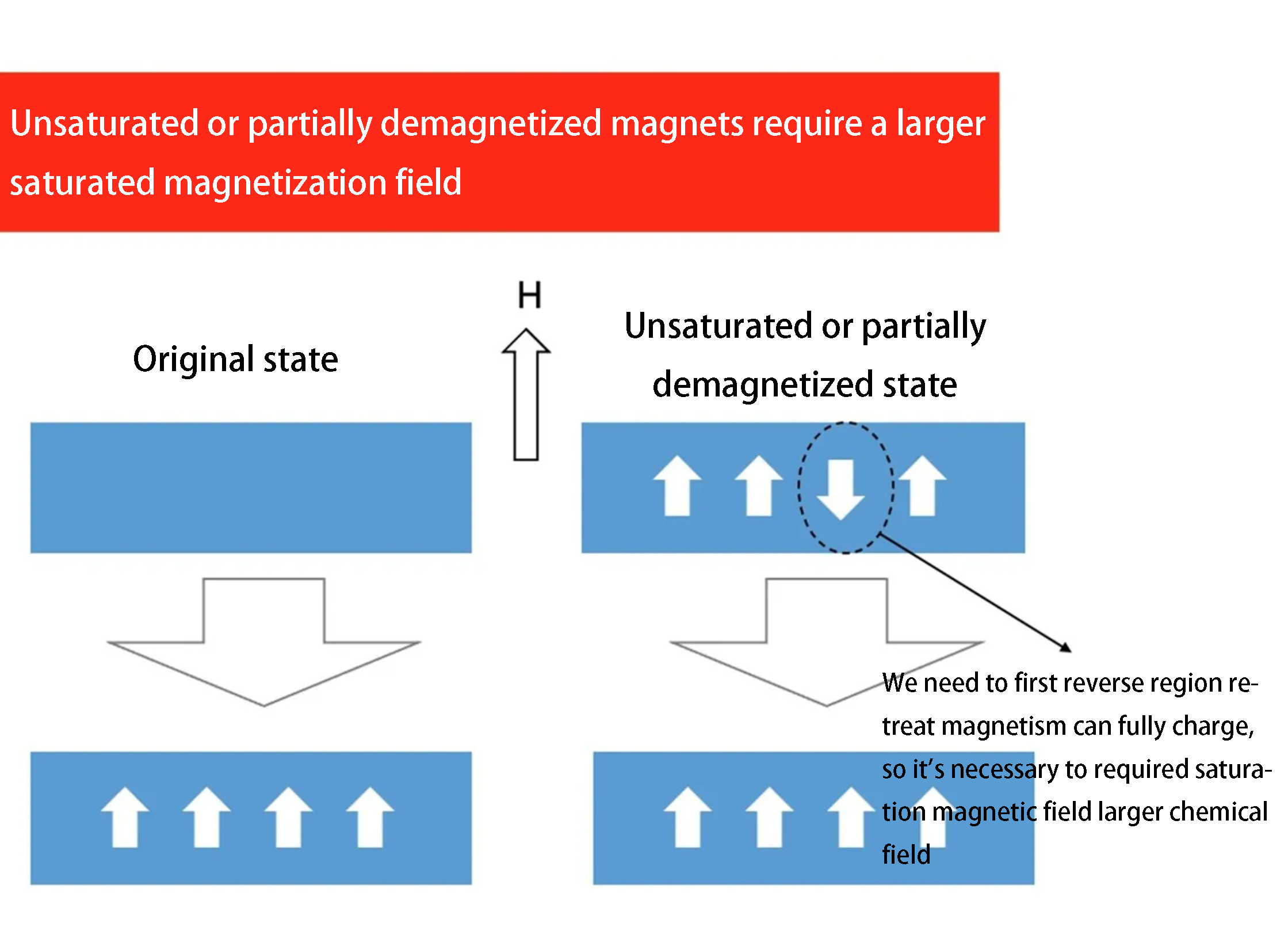
ਪੋਸਟ ਟਾਈਮ: ਅਗਸਤ-18-2023